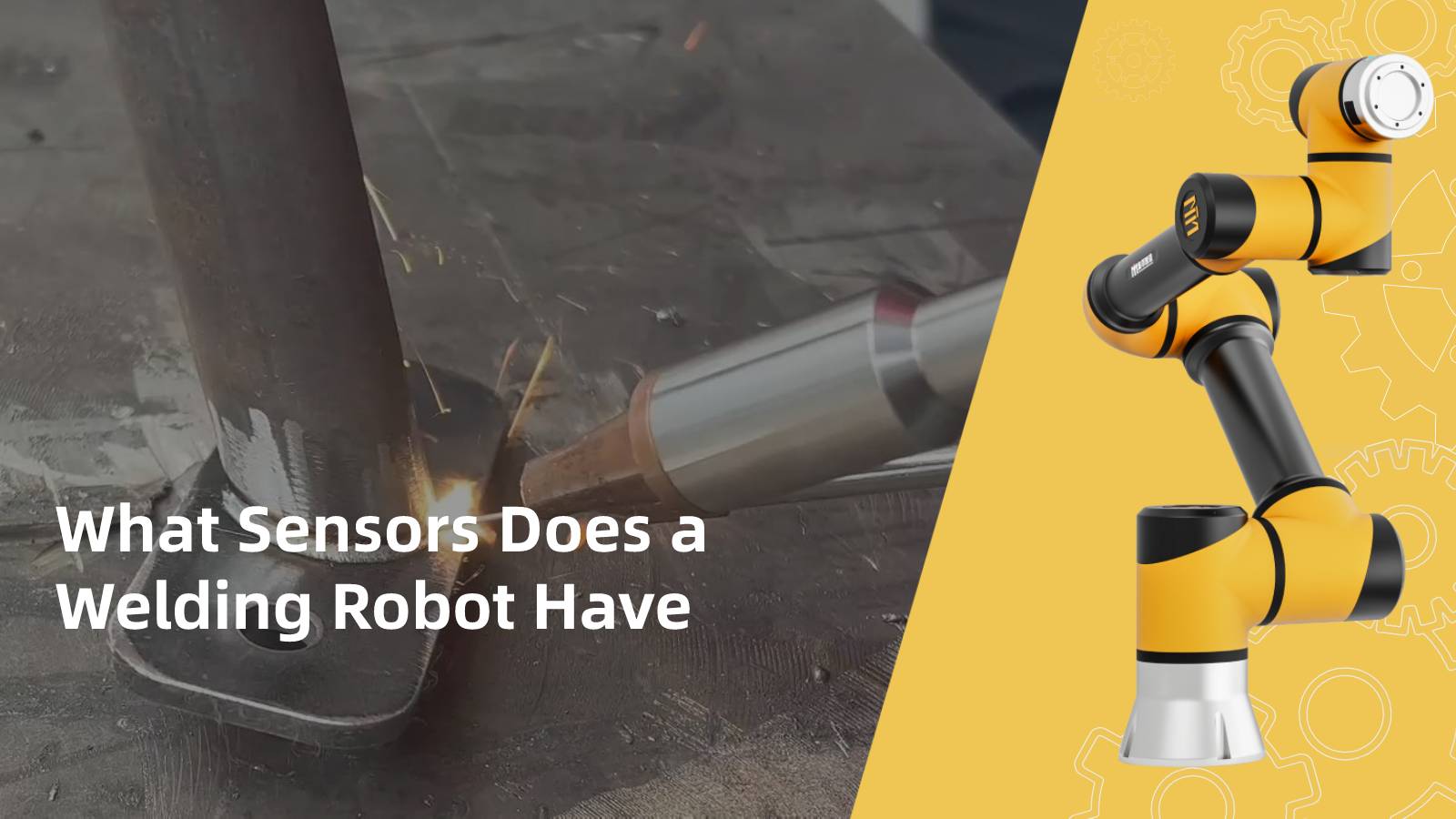
In the realm of industrial automation, welding robots have emerged as indispensable tools for enhancing precision, efficiency, and safety in welding processes. These robots are equipped with an array of sensors that enable them to perform tasks with remarkable accuracy and consistency. Let's explore some of the essential sensors utilized in welding robots: